Ten years ago Mulberry was staring down the barrel of a serious problem. The British design house, known for its lineup of high-end It handbags, had an age issue: More than 50 per cent of its 600 factory employees were over 50 years old – 13 per cent were over retirement age. For a brand that relies on skilled craftspeople to produce over 200,000 bags annually, these are the kind of figures that set off alarm bells. "We are the largest manufacturer of luxury leather goods in the U.K., but we had a very traditional set up at the time," says group production and sourcing director Rob Billington, who oversees the company's two Somerset factories. "Only 30 per cent of our workforce were under 40. We needed to do something about it and fast."
In 2006, Mulberry launched its now award-winning apprenticeship scheme. In partnership with Somerset's Bridgwater and Taunton College, the year-long program invites 10 to 12 students to the factory to be trained in leather goods manufacturing. At the end of 12 months, the apprentices are awarded a technical certificate and become full-fledged craftspeople. So far, 100 apprentices have gone through the program and 75 have stayed on as full-time employees. Today, only 20 per cent of Mulberry's factory workers are over the age of 50, 40 per cent are under 35, and the average age is now 38. "It's a much more sustainable situation to be in," says Billington. "Not only have we transformed the age demographic in the business but we're continuing our tradition of heritage skill, which is so important to the brand."
Mulberry isn't the only fashion house dealing with aging artisans and the potential demise of traditional craftsmanship. With interest in trades and manual work waning, many brands have started taking steps to save the industry from collapse. Chanel has slowly been acquiring struggling savoir-faire maisons, including embroiderer Lesage, plumassier Lemarié and milliner Michel. Swiss watchmaker Chopard launched a school in 2008, which runs a four-year intensive apprenticeship program that covers everything from watch- and jewellery-making to polymechanical, micromechanical and surface finishing. In 2013, Brunello Cucinelli, the high-end Italian label famed for its luxurious cashmere sweaters, established its School of Arts and Crafts at its headquarters in Solomeo.
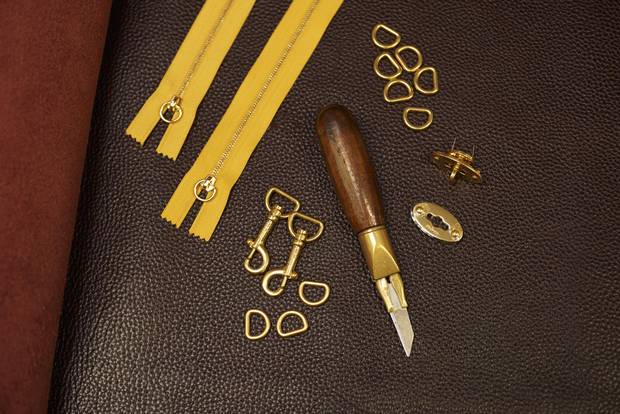
Tools and accessories at a Mulberry facility.
Currently, in an effort to further support U.K. manufacturing, Mulberry has taken a leading role in developing a broader apprenticeship model that can be adopted by other British leather-goods companies. "The stronger the leather industry is in the U.K., the stronger our company will become," says Billington. "Over the past few years the world has tried to put every kid into college and as a consequence we're losing these vocational skills. We've got a responsibility both locally and within the broader industry to bring that back."
In addition to helping secure the future of fashion, these programs are offering young people a legitimate, even lucrative, career option. "I've got one former apprentice, Harrison Malik, who joined when he was 17, six years ago. He's now a development specialist, which means he's working alongside our two Italian master craftsmen, who have 40 years of experience between them," says Billington. "He's our 23-year-old English master craftsman." It's worth mentioning, too, that Malik is now earning more than his former school mates who at this point are just finishing university and struggling to find work in a crowded job market. "People are starting to see us as a real alternative to going to university," says Billington. "We have quite a long waiting list of people wanting to become apprentices."
Malik sees apprenticing as an appealing substitute to post-secondary education – perhaps even more advantageous given it's a paid position. "It gives people the opportunity to continue their education in a chosen industry whilst earning a salary," he says. "As well as this, it gives young people that don't envisage going to university another career path to consider. I have been given the opportunity to gain a skilled trade and achieve further qualifications whilst embarking on a career that will give me further opportunities to develop."
Traditional artisan industries may not exist in Canada at a large scale anymore, but according to Dorie Millerson, chair of material art and design at OCAD University in Toronto, there is increasing interest from young people in craft and handmade goods here as well. "There is absolutely a growing movement towards craft skills, particularly in fashion," she says. "A lot of design students today want an active role in their creative careers. They want to work with their hands and learn how to make something themselves."
Modern craftsmanship ventures beyond technical skills like mending, embroidery or metal smithing, into the world of ideas and innovation. "Every year our students are more and more interested in creating something new or incorporating technology into their work," says Millerson. One student is creating her own fabric from recycled and repurposed materials; another is designing digitally enhanced clothing for people with Alzheimer's. "It's like a modern version of an artisan. Someone who both designs and makes," she says.
Mulberry, too, is finding that innovation is an unexpected but welcome benefit of its newly youthful workforce. "I love how we have a mix of ages together on the same floor," says creative director Johnny Coca. "The old generation tells the new generation about the traditions of the past, and the young workers bring ideas and something quite new and fresh."
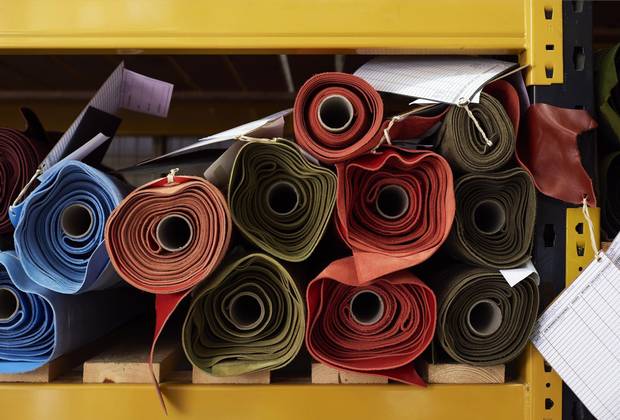
Raw material at a Mulberry leather facility.
Itching to stitch
From whisky to watches, many iconic brands rely on apprenticeship programs to encourage fledgling makers and production facilitators.
Louis Vuitton
The legendary French house opened its doors to students at the Parisian CFA de la Bijouterie Joaillerie in 2014 through a concurrent program where apprentices combine classroom education with technical training within Louis Vuitton's jewellery department. The program runs as a part of the a collaboration between Louis Vuitton's parent company, LVMH Moët Hennessy Louis Vuitton SE, and expert trade schools in selected métiers: watchmaking, winemaking and leather goods. Students gain experience as they meet and work with professional artisans working in the field and in 2016, 100 per cent of the cohort earned their degrees.
Dior Couture
Also through the LVMH-run Institut des Métiers D'Excellence, Dior Couture runs programs in its tailoring and draping ateliers with students from the famed École de la Chambre Syndicale de la Couture Parisienne, whose graduates includes designers Karl Lagerfeld, Valentino Garavani and Yves Saint Laurent. Applicants to the two-year program are between the ages of 16 and 24, in accordance with French labour laws. Apprentices are expected to assemble a full garment, complete with hand-sewn finishes at the end of the program and receive a certificate of professional aptitude.
International Watch Co.
Like other Swiss watchmakers, the IWC offers a four-year specialization in the assembling and servicing of its watches, of which the first three years incorporate basic training in manufacturing tools and the step-by-step assembling of simple mechanical and electronic watches, while the final year tackles watch repairs and more complicated timepieces. Candidates can enter the program immediately after high school, provided they can show good performance in the study of physics, mathematics and technical drawing. These apprenticeships continue the traditions of Swiss watchmaking.
Burberry
The British have been forerunners in the manufacturing of quality wool, footwear and leather for centuries, and Burberry, a global face of British design, has been a contributor to this tradition since 1856. As such, to retain a focus on British heritage, the company has developed a system of on-the-job training opportunities to improve an apprentice's skills, business acumen and future employability at factories in Castleford, Keighley and Blyth in the United Kingdom. The first phase of the Burberry Apprentices program works towards developing young people globally in the company's retail, internal manufacturing and distribution sectors.
The Macallan
With the digitization of many industries, manufacturers like Scotland-based Edrington, parent company of The Macallan, increasingly employ engineers to ensure the smooth running of machinery. While whisky-making apprenticeships are in the pipeline at the manufacturer, the company currently develops its engineering department through an internal graduate scheme and student placements through Saltire Scholar, a program that connects undergraduate students at Scottish universities to businesses in the region. Although headquartered near Glasgow, the engineers have the opportunity to experience the company's craftsmanship at the production facility in Craigellachie where whisky is produced and aged.
Ross Dias
Visit tgam.ca/newsletters to sign up for the Globe Style e-newsletter, your weekly digital guide to the players and trends influencing fashion, design and entertaining, plus shopping tips and inspiration for living well. And follow Globe Style on Instagram @globestyle